Industry-Leading Membrane Switch Manufacturer with ISO Certification
Discovering the Production Refine of Membrane Switch for Numerous Industries
The production process of Membrane buttons is an intricate venture that requires accuracy and interest to detail. From choosing suitable materials to executing rigorous quality assurance steps, each step plays a vital function in ensuring performance. Numerous markets, including automobile and clinical, depend on these components for their distinct applications. Understanding the details of this procedure reveals considerable insights right into exactly how these switches are created and their impact throughout varied sectors.
Understanding Membrane Changes: An Overview

Secret Materials Used in Membrane Switch Manufacturing
In Membrane button production, the selection of essential products substantially influences functionality and toughness. Conductive materials, adhesives, and layers play crucial roles, while substratum selection influences general efficiency and reliability. Comprehending these elements is crucial for optimizing the style and manufacturing of Membrane buttons.
Conductive Materials Introduction
Conductive materials play a crucial function in the capability of Membrane switches, making certain trustworthy electric links within the device. Frequently utilized products include silver, copper, and carbon-based inks, each offering unique benefits. Silver is favored for its high conductivity and toughness, making it perfect for applications needing robust performance. Copper, while somewhat less conductive than silver, is a cost-effective alternative commonly made use of in published circuits. Carbon-based inks provide a versatile alternative, suitable for applications where flexibility and lower costs are prioritized, although they have lower conductivity compared to metal alternatives. The choice of conductive products directly impacts the overall reliability, lifespan, and performance of the Membrane button, making it an essential factor to consider in the production procedure.
Adhesives and Coatings
Adhesives and coverings are crucial components in the production of Membrane switches, giving vital bonding and protective buildings. These materials ensure that various layers of the switch, including graphic overlays and circuitry, stick firmly to each other, boosting resilience and functionality. Frequently utilized adhesives consist of pressure-sensitive adhesives (PSAs) and epoxy-based formulas, which use strong adhesion and durability. Coatings, such as polyurethane or acrylic, serve to shield versus ecological variables, consisting of moisture, abrasion, and chemicals. Furthermore, coverings can enhance responsive responses and aesthetic allure, contributing to the general user experience. The option of suitable adhesives and coverings is critical for maximizing efficiency and long life in diverse applications across numerous markets, ensuring that Membrane switches fulfill certain operational demands.
Substrate Option Aspects
Substrate choice plays an important function in the production of Membrane buttons, as it significantly influences their total efficiency and durability. Trick materials such as polyester, polycarbonate, and versatile published circuit card (FPCBs) are typically utilized for their unique residential or commercial properties. Polyester is preferred for its cost-effectiveness and resistance to abrasion, making it appropriate for applications with high wear. Polycarbonate deals exceptional quality and influence resistance, ideal for environments needing high visibility. FPCBs supply improved flexibility and are often used in complicated layouts. The choice of substrate additionally affects aspects like thermal stability, chemical resistance, and simplicity of printing. Inevitably, picking the suitable substratum is essential for making sure the capability and longevity of Membrane changes across different sectors.
The Layout Process of Membrane Switches Over
The layout process of Membrane switches is an important phase that significantly affects the capability and visual appeals of the end product - membrane switch manufacturer. It starts with defining the particular needs of the application, including measurements, switch layout, and tactile feedback preferences. Designers should take into consideration individual communication, making certain that the button is intuitive and accessible.Next, products are chosen based on resilience, adaptability, and ecological resistance. The combination of graphics and branding components is also important, as it improves visual allure and communication. Prototyping permits iterative screening, allowing modifications based upon customer comments and efficiency evaluations.Additionally, the style should account for the electrical parts, such as ports and circuits, making sure reliability and simplicity of usage. Ultimately, an effective design harmonizes performance, aesthetics, and user experience, leading the way for reliable manufacturing and long-lasting performance in different industries
Printing Methods for Membrane Switches
The printing strategies utilized in Membrane button manufacturing play an essential role in figuring out the end product's high quality and performance. Screen printing uses advantages such as sturdiness and lively shade application, while electronic printing developments give flexibility and accuracy in design. Comprehending these techniques can significantly influence the overall performance of Membrane buttons in different applications.
Display Printing Advantages
Countless benefits make screen publishing a recommended technique for generating Membrane buttons. This method permits premium, dynamic shades and in-depth layouts, which are necessary for user interface applications. Display printing is specifically effective for applying thick ink layers, boosting toughness and responsive responses. On top of that, it provides outstanding bond to different substrates, making sure long life in requiring settings. The procedure is economical for huge manufacturing runs, as it decreases setup time and waste. Display printing supports a vast range of inks, including specialty and UV-curable options, allowing convenience in style. Its capability to generate consistent results across multiple units makes it a trustworthy selection for manufacturers click over here going for quality and efficiency in Membrane switch production.
Digital Printing Innovations
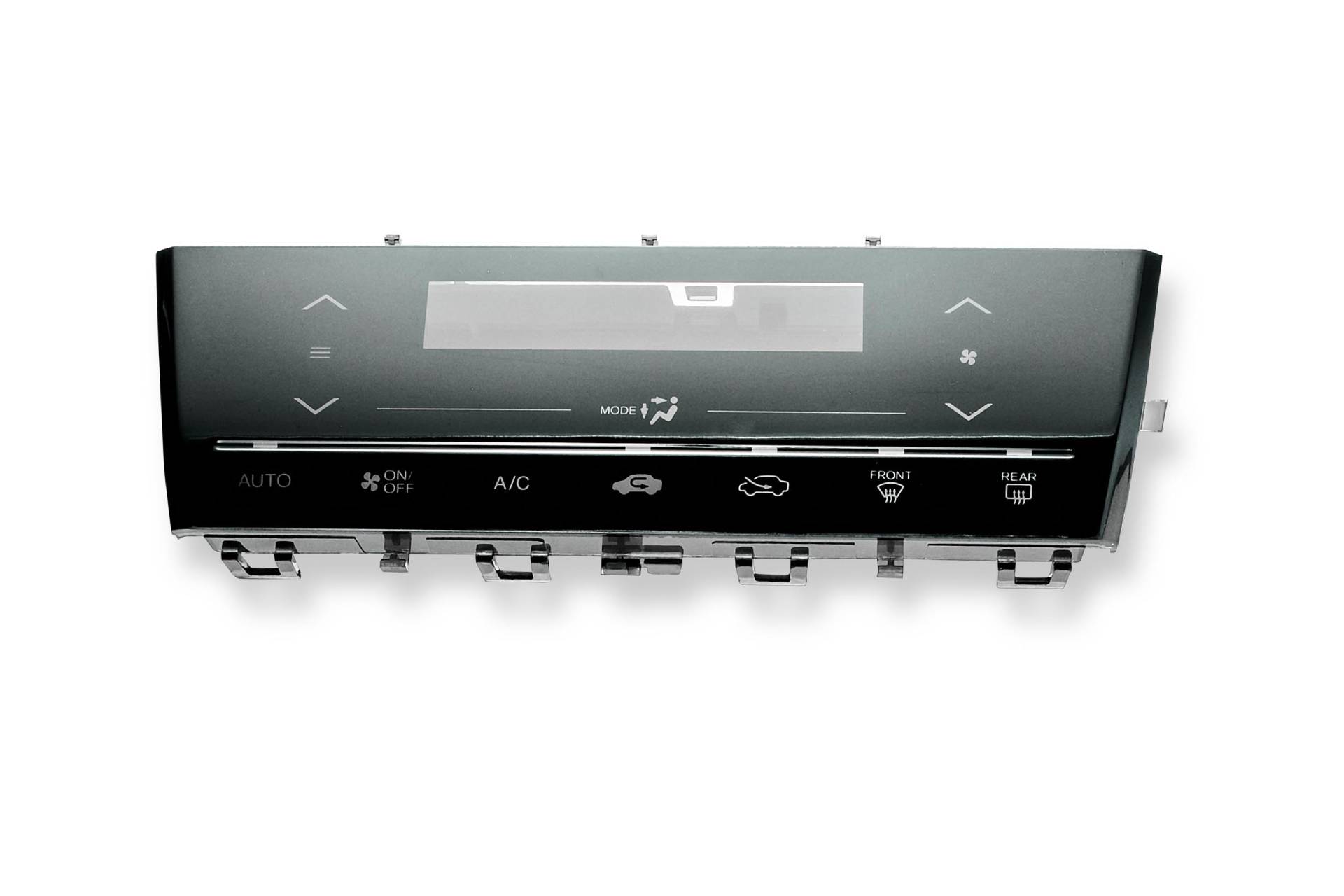
Developments in digital printing modern technology are changing the production of Membrane switches, offering suppliers cutting-edge remedies that boost layout flexibility and performance. Digital printing permits intricate styles and high-resolution graphics, allowing customized branding and capability without the limitations of traditional techniques. This method reduces setup times and costs, promoting shorter manufacturing runs and minimal waste, making it suitable for businesses with varying needs. In addition, developments in ink solutions supply much better resilience and adhesion, making certain longevity in numerous environments. As industries progressively look for tailored and complicated layouts, electronic printing stands out as an essential method, setting a brand-new criterion in Membrane switch manufacturing. The assimilation of these developments settings producers to fulfill progressing market requires properly.
Setting up and Layering of Membrane Switch Elements
Mindful setting up and layering of Membrane button elements are essential to guaranteeing performance and sturdiness. This procedure starts with the precise positioning of various layers, including the visuals overlay, adhesive, circuit layer, and backing product. Each component needs to be carefully placed to keep electrical honesty and interface responsiveness.During setting up, conductive traces are related to the circuit layer, generally made from materials like polyester or polycarbonate. This layer is critical, as it sends signals when pressure is used. The adhesive utilized for bonding these layers is additionally chosen for its capability to withstand environmental stresses while preserving a protected bond.Heat and pressure are often used during the setting up process to ascertain that the layers stick appropriately without jeopardizing the performance of the button. Focus is offered to the side sealing to safeguard versus wetness and contaminants, securing the longevity of the Membrane switch in various commercial applications.
Quality Assurance Steps in Membrane Switch Manufacturing
Quality control actions play an essential function in ensuring the reliability and efficiency of Membrane switches adhering to the setting up and layering of their elements. In the production procedure, a number of crucial inspections are performed to support my explanation high quality requirements. These consist of visual assessments for flaws in printing and sticky application, along with useful tests to validate the responsiveness of each switch.Additionally, environmental testing is performed to evaluate the buttons' toughness against temperature variations and moisture direct exposure. Manufacturers usually carry out statistical process control (copyright) methods to keep an eye on manufacturing uniformity, enabling very early detection of anomalies.Furthermore, traceability systems are developed to track products and components, making sure responsibility and assisting in recalls if essential. Calibration of tools and adherence to sector standards are also crucial to maintaining item honesty. Jointly, these quality control actions guard the performance of Membrane changes throughout numerous applications, eventually boosting client contentment.
Applications of Membrane Switches Across Different Industries
Membrane switches are used across a varied range of markets, showcasing their adaptability and flexibility. In the medical market, they provide waterproof and reputable user interfaces for devices such as analysis tools and infusion pumps, guaranteeing health and ease of use. The vehicle sector utilizes Membrane switches for dashboard controls, making it possible for smooth communication between the vehicle driver and lorry systems.In customer electronics, these switches are found in home appliances and portable gadgets, providing a streamlined, contemporary visual while enhancing functionality. Industrial applications also take advantage of Membrane switches for equipment control panels, where toughness and resistance to extreme conditions are essential.Furthermore, the aerospace and protection sectors make use of Membrane switches for cabin instrumentation and communication systems, prioritizing integrity and efficiency under severe conditions. In general, Membrane switches play a vital duty in boosting the user experience and operational efficiency across different domain names.
Frequently Asked Questions
How much time Does It Require To Manufacture a Membrane Switch?
The production time for a membrane switch commonly ranges from a couple of days to numerous weeks - membrane switch manufacturer. Factors affecting this duration consist of layout intricacy, material schedule, and manufacturing volume, all impacting the overall timeline markedly
What Is the Typical Life Expectancy of a Membrane Switch?
The typical life-span of a membrane switch generally ranges from 1 additional hints to 5 million actuations, depending on aspects such as material top quality, ecological conditions, and use regularity, significantly influencing toughness and overall efficiency.
Can Membrane Switches Over Be Custom-made for Certain Applications?
Membrane switches can without a doubt be personalized for certain applications. Their style flexibility allows for changes in dimension, shape, shades, and graphics, making certain compatibility with unique demands throughout numerous sectors and enhancing performance and individual experience.
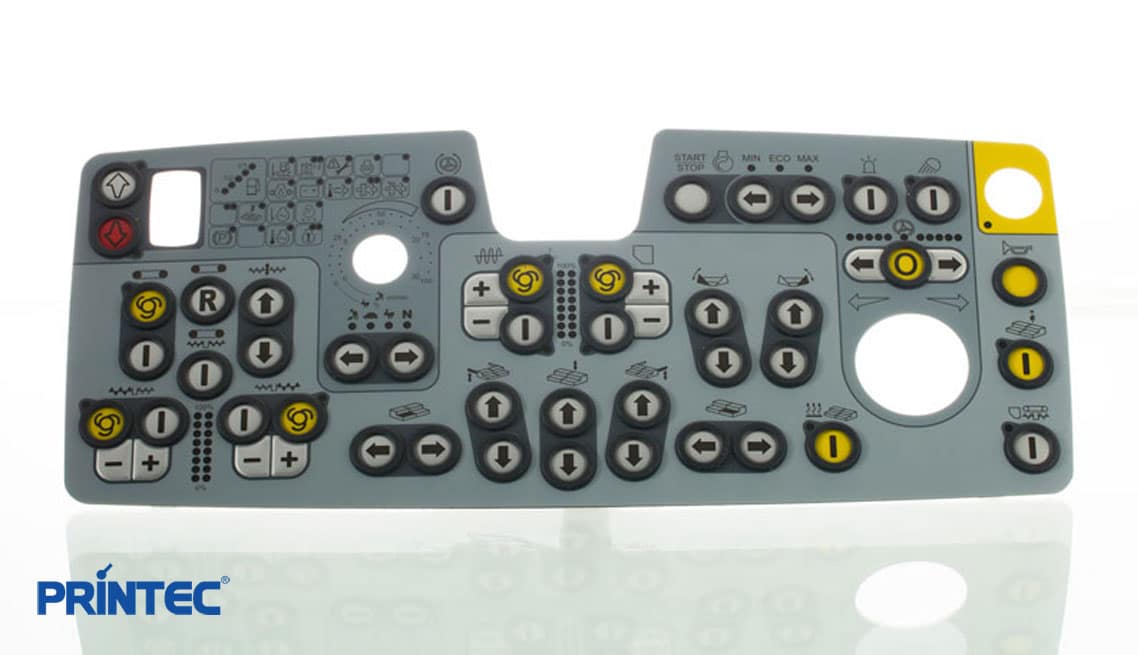
Are Membrane Changes Environmentally Friendly?
The ecological influence of Membrane switches over varies. Some products utilized may not be green, while improvements in producing processes are increasingly concentrating on sustainability, aiming to decrease waste and advertise recyclable elements in their production.
What Are the Usual Failure Modes of Membrane Switches?
Usual failing settings of Membrane switches include delamination, sticky failing, deterioration from use, dampness ingress, and electric failures. These concerns can significantly influence functionality, performance, and lifespan in various applications throughout various sectors. Membrane buttons can be customized to fit details style needs, such as form, size, and functionality, making them very adaptable.The construction normally entails multiple layers, including a graphic overlay, sticky, and a circuit layer, which work together to create a seamless user experience. In Membrane switch manufacturing, the option of essential products substantially affects capability and durability. The automotive market uses Membrane switches for control panel controls, allowing smooth interaction between the driver and vehicle systems.In customer electronic devices, these buttons are located in home appliances and handheld tools, supplying a smooth, modern-day visual while enhancing functionality. Industrial applications additionally leverage Membrane switches over for machinery control panels, where sturdiness and resistance to extreme conditions are essential.Furthermore, the aerospace and defense sectors utilize Membrane buttons for cockpit instrumentation and communication systems, prioritizing dependability and performance under extreme problems. Membrane buttons can undoubtedly be customized for details applications.